- Tube Ice Plant Solution
- Aluminum Direct Cooling Block Ice Plant Solution
- Brine Cooling Block Ice Plant Solution
- Flake Ice Plant Solution
- Artificial Skiing Ground Solution
- Chemical Reactor Cooling Solution
- Concrete Cooling Solution
- Edible Ice Station Solution
- Mine Cooling Solutions
Contact Us
- +86 21 57456563
- +86 21 57456583
- inquiry@linskyice.com
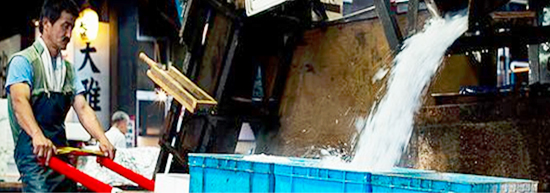
Concrete is one of the most important civil engineering materials in contemporary. The main raw materials of concrete contain cement, sand and gravel. Different grades of concrete depend on the proportion of raw materials. In the casting process for large buildings, such as mansions, dams and nuclear power projects, large areas of concrete stacked, so that internally generated considerable stress. In order to prevent its cracking due to large stress and ensure the strength of concrete casting, the concrete cast temperature should be strictly controlled. Research and a lot of empirical data show that the mixed concrete temperature maintained at 25 ~ 28°C is appropriate. However, as the barn (storage room of sand, gravel and etc) was long-time exposure to sun, raw materials easily absorb the surrounding heat and solar radiation heat. So the temperature of the raw material could have already exceeded 25°C; while in the mixing process, the mixer power consumption plus heat generated by chemical reaction would both again raise the temperature of the concrete.
In response to the above circumstances, Linsky has mastered a complete set of concrete cooling solutions, which apply to the global climate, including tropical, desert high temperature areas. Even in the case of ambient temperature above 45°C, Linsky is still able to ensure the appropriate concrete temperature when it is out of station.
Depending on the environmental conditions, customers can select part of or all of processes as following to meet concrete cooling requirements:
Concrete Cooling Method One: Aggregate Pre-Cooling Solution
Aggregate pre-cooling: in some hot areas, aggregate (sand and gravel etc) is pre-cooled in compartment before entering the mixer. The cooling temperature is specific upon request.
Linsky pre-cooling compartment can be classified into evaporative-cooled, air-cooled and water-cooled ones.
Evaporative-cooled air pre-cooling compartment doesn't need refrigeration system. Air is humidified and cooled by using evaporative cooling tower. Part of the water is evaporated so that the air temperature is lowered to near the dew point temperature. Afterwards, the cooled air is supplied to the cooling compartment to pre-cool the aggregate. Evaporative pre-cooling compartment is suitable for the relatively dry environment, areas with low dew-point temperature, generally speaking it could lower the temperature of the aggregate by 5 ~ 10 °C. Evaporative pre-cooling compartment is a more energy-efficient pre-cooling measure by using the natural way of cooling. But this method has limited cooling capacity and needs to be used with water chiller and ice machine.
Low-temperature cold air pre-cooling compartment is equipped with refrigeration system. The air will flow the evaporator part in the refrigeration system and be directly cooled down to the specified temperature for example, the ambient temperature of the air is reduced from 45 °C to 10 °C. Then the cold air enters into the low-temperature cold air compartment. To obtain a sufficient heat exchange between aggregate and cold air, the conveyor belt is designed in detour. In this case, cold air of 10 °C can directly lowered the temperature of aggregate below than 18 °C, so the mixed concrete obtains lower outbound temperature. The evaporation temperature of its refrigeration system is at around 0 °C, at high evaporation temperature, the compressor can be obtained a higher COP value, which is more energy-efficient than ice cooling method.
Low-temperature cold water pre-cooling compartment is equipped with a low temperature chiller. Linsky low temperature chiller provides cold water of 0.5 °C (near freezing point). Then the cold water is utilized to spray on the aggregate conveyor, so the aggregate temperature can be rapidly reduced to the specified degrees. The aggregate will be drained on the conveying belt before enters into the mixer. Low-temperature cold water pre-cooling compartment can cool aggregate to 10 °C or below and low-temperature cold water can be recycled after filtered.
Concrete Cooling Method Two: Mixed Water Cooling Solution
Raw material of concrete includes not only concrete cement, sand and gravel, as well as a certain percentage of water. Mixed water cooling solution is adding low temperature cold water or ice in material mixing process. It is an effective concrete cooling measure. Due to a small proportion of water in the concrete composition, if at high ambient temperature region, adding cold water or ice may still not reach cooling requirements, so cold water shall be combined to use with pre-cooling compartment. In this case, please consult our technical service engineers to get the exact solution.
Chilled Water Cooling: Linsky low temperature water chiller can offer ultra-low temperature cold water which is very close to the freezing point of 0.5 °C for the mixer. It is a perfect solution for even the hottest desert regions, in the case of the water temperature up to 45 °C, the outlet water temperature can reach down to around 0.5 °C. Due to a small proportion of water in the concrete composition, adding cold water may still not reach cooling requirements, which usually need to be combined to use with ice machine or pre-cooling compartment.
Ice and Water Cooling: Ice is water in solid state, with latent heat up to 335kj / kg. It is the substance in nature that can store max cooling capacity per unit. In concrete cooling, ice can help effectively reduce the mixing temperature of the concrete. And in various ice machines, flake ice machine is widely and mostly used. Ice produced by flake ice machine is in scale shape, very close to powder state so that it could evenly cools down the object and maintains temperature balance in the process of concrete mixing. This feature makes it popular in concrete application. The adoption of Ice and water cooling method needs an ice station to supply ice. The main parts of a typical ice station include containerized flake ice machine, rake type automatic ice storage, screw ice conveying system and ice weighing system.
Containerized flake ice machine: concrete mixing station is always set up in the open-air place, so containerized ice machine is very necessary. Linsky containerized flake ice machine can support outdoor work, even in the dusty weather, heavy rain and strong winds climate, it is still able to run. The maximum capacity of single unit of Linsky containerized flake ice machine is 60 tons / day. To meet larger capacity requirements, multiple units of containerized flake ice machine can be combined to use.
Rake type automatic ice storage pave ice flake flat inside of ice storage and could hold ice at max capacity. It also can convey ice to the ice outlet according to actual ice demand. It is usually installed under containerized flake ice machine. The ice flakes produced by ice machine falls off into containerized rake type automatic ice storage from the bottom of flake ice machine. Because it is equipped with refrigeration unit, so the ice storage temperature could be kept below -10°C, which can always keep ice flake dry. The rake teeth of automatic ice storage can further crush ice flake into powder and forms snow.
Screw ice conveying system: Screw ice delivering system is the most commonly used in concrete cooling. The longest transmission distance of Linsky screw ice conveyor could be up to 50 meters in single piece, with the highest elevation angle of 45 degrees.
Ice weighing system: Linsky weighing machine can be divided into screw weighing machine, pneumatic weighing machine and crawler weighing machine, the commonly used one is the screw weighing machine. Our weighing machine can weigh 2 tons maximum at one time.
Copyright © All rights are reserved by Linsky• Formulate future since 2004